Sala de jarabe
SEPPELEC diseña e instala la sala de fabricación de la nueva planta embotelladora de COCA COLA FEMSA, considerada una de las fábricas de bebidas más sostenible del mundo.
Coca Cola FEMSA, el mayor embotellador independiente del mundo, inauguró el pasado 5 de junio la planta de fabricación de bebidas no alcohólicas más moderna de América Latina, el acto fue dirigido por José Antonio Fernández, Presidente Ejecutivo del Consejo Administrativo de FEMSA, en compañía del Presidente de la República de Colombia, Juan Manuel Santos y altos ejecutivos de Coca Cola Company.
Con una inversión de 250 millones de dólares, la planta ubicada en el Parque Industrial FEMSA, cuenta con 60 mil metros bajo techo y es considerada la planta más eficiente del sistema Coca Cola.
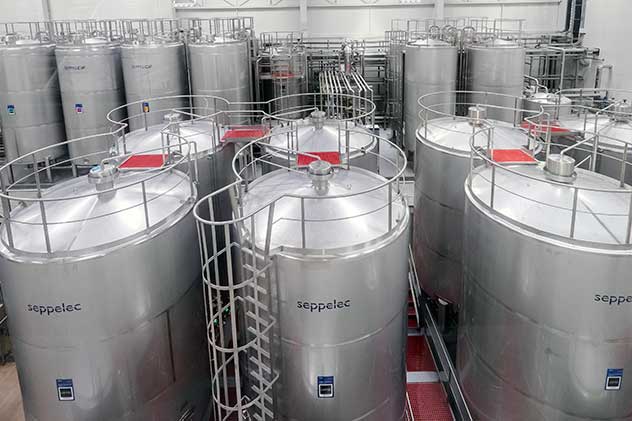
John Santa María, Director General Coca-Cola FEMSA, ha declarado que “La nueva planta es un ejemplo de ingeniería punta, eficiencia y sostenibilidad”. La innovación en tecnología permitirá el ahorro de entre el 20 y el 30% en el uso de agua y un 20 a 40% de ahorro de energía. Un ejemplo de productividad, sostenibilidad y mínimo impacto ambiental.
Seppelec ha participado de manera decisiva en el proyecto con su ingeniería más avanzada, suministrando la sala de jarabe completa, compuesta por equipos Vacbid de vaciado de concentrados, Lotmix para disolución de sólidos y Sepmix para el blender en continuo; actualmente cuenta con 2 líneas de embotellado de alta capacidad que producen 75 millones de cajas al año. Además, Seppelec ha suministrado 2 sistemas de limpieza CIP, 1 pasteurizador para zumos y un mezclador continuo de alta capacidad para producción de Coca Cola.
En una segunda fase, iniciada en julio de 2015, Seppelec ha comenzado la instalación de 3 líneas más de capacidad media, con una producción prevista de 55 millones de cajas al año.
Equipos para vaciado de concentrados VACBID, más rendimiento e higiene en la fabricación de zumos.
Desde sus inicios como empresa, SEPPELEC ha prestado una especial atención a los equipos de vaciado de pulpa y fruta concentrada, esta fase del proceso de fabricación de zumos ha sido tradicionalmente uno de los cuellos de botella de las líneas de producción.
En efecto, la alta viscosidad de estos productos, su manejo a muy baja temperatura, las características de los envases: bolsa plástica en bidón metálico, cubitainers, garrafas, etc. hacían que la operación de vaciado fuera a menudo muy trabajosa para los operadores, lenta en cuanto a capacidad de fabricación, y que por las características del envase, ponía en riesgo a menudo la higiene del proceso y ocasionaba pérdidas de materia prima importante. Los sistemas de bombeo empleado (las ruidosas bombas neumáticas o las de tornillo excéntrico) eran un quebradero de cabeza para los técnicos de mantenimiento que debían reparar y substituir a menudo membranas y estatores, cuando no buscar sus fragmentos en el producto.

SEPPELEC se propuso desarrollar una máquina que resolviera todos estos inconvenientes, y fruto de una labor de desarrollo y experimentación de años, es la línea de equipos VACBID (tecnología patentada). Los diferentes modelos de VACBID han conseguido en primer lugar dar la capacidad que exigen las líneas de producción actuales, consiguiendo cadencias de hasta 25 bidones/h.
En segundo lugar, son equipos polivalentes para cualquier concentrado, por viscoso que éste sea. Los VACBID están vaciando con excelentes resultados bidones de los concentrados de pulpa más viscosos: Melocotón, Mango, Tomate… La capacidad de vaciado se optimiza además por programación para cada producto.
En tercer lugar la laboriosidad de la operación se ha simplificado enormemente: el operador actual sólo debe aproximar el bidón bajo la máquina, abrir la bolsa y sujetarla en las abrazaderas de la máquina. El resto de las operaciones: descenso de la lanza, cebado de la bomba, aclarado de la bolsa, apurado del contenido, se realizan de forma automática.
La especial concepción de la máquina que levanta la bolsa dentro del barril para aclarar toda su superficie a alta presión, reduce al mínimo las pérdidas de producto.
La higiene de la operación se ve muy favorecida, pues no hay contacto del operador con el tubo de vaciado, y todas las superficies en contacto con el producto se limpian al final de la producción mediante sistema CIP en una carcasa dispuesta a tal efecto.
Por último, la concepción del sistema de bombeo, con rotor y estator en inoxidable, evita la incorporación de elastómeros al producto así como el mantenimiento correctivo que imponían las antiguas bombas: La bomba puede descebarse sin riesgo de ruptura de estator.
Existen distintos modelos de VACBID adaptados a sus necesidades de producción, si desea recibir información más detallada utilice el formulario de contacto y en unos días nos pondremos en contacto con usted.
Ecoproducción de bebidas refrescantes en España. Informe de sostenibilidad ambiental
La Asociación de Bebidas Refrescantes (ANFABRA) ha hecho público un informe en el cual se habla de las políticas medioambientales que el sector ha llevado a cabo para optimizar los procesos de producción reduciendo a su vez el consumo de agua y energía junto a la huella de carbono de cada empresa. Seppelec ha desarrollado unidades de producción que contribuyen a esta causa alcanzando niveles de optimización y ahorro considerables. En este post analizamos los cambios producidos y los objetivos de cara al año 2020 que se plantea la asociación en el ámbito energético y en el consumo de agua en los procesos.
CONSUMO DE AGUA
El agua es fundamental en las bebidas refrescantes. Es el principal ingrediente y, además, un recurso básico en los procesos de producción, para la limpieza de instalaciones y el cumplimiento de los estrictos requisitos de higiene y seguridad alimentaria. Los principales consumos se producen en la limpieza de equipos y conducciones y en el lavado y enjuague de envases. El ratio de consumo de agua (litro de agua consumida por litro de producto fabricado) es de 2.19 litros, casi la mitad de lo que se utiliza para producir otras bebidas, y se ha reducido en más un 8% en los últimos dos años. El objetivo es alcanzar una reducción del 20% del ratio para el periodo comprendido entre 2010 y 2020.
Las compañías del sector suelen disponer de contadores de agua independientes para cada proceso, para medir y hacer un seguimiento de cada uno de ellos. Estos contadores toman medidas periódicas y permiten conocer el impacto de las medidas de eficiencia implantadas, identificar posibles ineficiencias debidas a fallos en los equipos y comparar los consumos de un mismo proceso en distintas plantas embotelladoras. Gracias a esto último se identifican buenas prácticas que pueden aplicarse en otras plantas para optimizar el consumo de agua.
Seppelec, desde sus departamentos de ingeniería y de diseño de maquinaria ha introducido medidas encaminadas a reducir la cantidad de agua empleada en los procesos de producción de bebidas. Algunas de estas mejoras ya están operativas y cualquier productor puede beneficiarse de ellas, podemos destacar en este aspecto:
- Optimización general del ahorro de agua en el diseño de salas de proceso. Por ejemplo, desde Seppelec hemos conseguido que en la última sala de proceso instalada se alcance un ahorro del 30% en sus consumos de agua.
- Nuevos sistemas de limpieza CIP, más compactos y optimizados para reducir el consumo de agua que funcionan con sistema de analítica y control de consumos en tiempo real.
- Optimización del ahorro de agua de las unidades de producción:
- VACBID: proceso de vaciado de bidones de concentrados con mínimo consumo de agua.
- LOTMIX: alto rendimiento con un reducido consumo de agua en la incorporación de sólidos de difícil disolución gracias a su sistema de trabajo por integración.
- COMPACMIX: integra las dos unidades mencionadas anteriormente, lo que supone un ahorro tanto de agua como de energía al facilitar y agilizar la producción. Es un sistema compacto de fabricación de alto rendimiento.
- Mezcladoras: la gran precisión en la mezcla en continuo, la recuperación de productos por recirculación y la optimización de empujes hacen de nuestras mezcladoras SEPMIX un claro ejemplo de minimización de consumo de agua..
- Tratamiento de azúcar por intercambio Iónico: permite un ahorro de 30 a 50% de agua con respecto a otros tratamientos de decoloración, y además supone un ahorro importante en tratamiento de aguas dulces, ya que se genera poca cantidad.
CONSUMO ENERGÉTICO
La reducción del consumo energético es otra de las prioridades del sector y ha seguido un patrón descendente, con un ahorro del 10% en los últimos 3 años, pasando de un consumo medio de 0,48 MJ/litro a menos de 0,45 MJ/L. El compromiso del sector es reducir el ratio de consumo de energía un 20% entre 2010 y 2020.
El consumo más relevante es el de electricidad, la energía responsable del funcionamiento de la mayoría de los equipos, y que supone alrededor de la mitad del total, seguido del de gas natural. Los principales consumos se producen en los compresores de aire (utilizados principalmente para el soplado de envases) y en los sistemas de frío.
En el caso de Seppelec también se ha hecho hincapié en la optimización energética de sus equipos en los últimos años, una muestra de ello podemos verla en los siguientes equipos:
- Homogeneizadores: el HOMOGEN de Seppelec consume entre 25-30 kWh, mientras que uno convencional de alta presión consume entre 150-200 kWh.
- Disolución de azúcar: nuestro DISOMIX, unidad compacta de disolución en continuo, lleva a cabo la disolución de azúcar en el punto de descarga del silo, lo que elimina los sistemas de transporte neumáticos o hidráulicos, suponiendo un ahorro energético de hasta el 70% en estos casos.
- PASTEURIZADORES: El ECOPASTEUR de Seppelec permite un gran ahorro de energía por su gran superficie de intercambio de calor, generación de turbulencia y recuperación energética directa o indirecta. Esto se traduce además en un ahorro significativo de agua de empujes y de limpieza.
Al margen de estos dos aspectos principales, el informe de ANFABRA habla también de las medidas de optimización que el sector está llevando a cabo en el diseño sostenible de envases y del transporte de los mismos, la reducción del efecto invernadero, la minimización de los impactos indirectos y la concienciación del consumidor en el consumo sostenible.
Si desea acceder al informe completo puede descargarlo en este enlace.
Y por supuesto, si desea asesoramiento para optimizar los consumos en energía y agua de los procesos en sus fábricas de bebidas, no dude en ponerse en contacto con nosotros.
Nueva sala de proceso de jugos y bebidas NCB para la planta de Tepotzotlan de Coca Cola – Femsa
Ya está en funcionamiento la nueva sala de proceso que en Seppelec hemos proyectado junto a una instalación de limpieza CIP para Coca Cola Femsa en la localidad mexicana de Tepotzotlan.
El objetivo tecnológico del diseño era el de crear un nuevo estándar de fabricación de bebidas no carbonatadas y jugos para el cliente. La instalación está basada en el concepto exclusivo de SEPPELEC MSS de «proceso por líneas de envasado con mezcla final en continuo«; cada línea lleva un equipo compacto de fabricación propio que consigue optimizar enormemente la producción gracias a la sencillez de la instalación y a la gran cercanía del proceso y el embotellado, lo que consigue eliminar prácticamente las mermas; es lo que hemos definido como «fabricación directa, del bidón a la botella«.
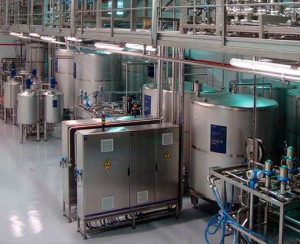
La instalación cuenta con equipos de proceso para:
Manejo de pulpas y jugos
Disolución de sólidos
Sistema de elaboración de bebidas
Área de jarabe simple
Recepción de fructosa
Rack de tuberías de proceso y servicios
Así mismo, se implantó un sistema integral de automatización de todo el proceso de fabricación que abarca la clasificación y control de las materias primas, el desalmacenaje de los componentes y la gestión de la receta.
Entre las ventajas que el sistema MSS de Seppelec le aporta al cliente podemos destacar:
Gran reducción de mermas en el manejo de pulpas y el proceso de producción.
Disolución de sólidos en línea.
Funcionamiento casi totalmente automático, a excepción de la preparación de estabilizantes.
Bajos costes de utilización y mantenimiento.
Control y gestión integral del proceso productivo.
Aumento de la higiene en el proceso productivo.
Aumento de la precisión en las fabricaciones.
Aumento del rendimiento.
Disminución de la necesidad de limpieza CIP, al fabricar productos similares en cada línea.
Optimización del espacio.
Reproducibilidad y trazabilidad.
Ahorro energético.
Fácil adaptación a modificaciones.
En la presentación posterior puede encontrar una información más detallada del proyecto; si desea ampliar información sobre el sistema de fabricación de bebidas MSS no dude en ponerse en contacto con nosotros.